Wśród naszych klientów często powtarza się pytanie, które w skrócie można by sformułować:
czy punkt 8.1.1 z specyfikacji ISO/TS 16949 należy interpretować w taki sposób, że dla każdego wyrobu produkowanego w procesie technologicznym należy wyznaczyć i umieścić w planie kontroli charakterystykę SPC, co wiąże się z koniecznością prowadzenia minimum jednej karty SPC dla każdego wyrobu?
Wyjaśnienia zacznijmy od stwierdzenia, że punkt 8.1.1 specyfikacji ISO/TS mówi:
8.1.1 Identyfikacja narzędzi statystycznych
W trakcie zaawansowanego planowania jakości dla każdego procesu powinny zostać określone odpowiednie narzędzia statystyczne i włączone do planu kontroli.
Warto tu zwrócić uwagę, że polskie tłumaczenia norm nie zawsze odzwierciedlają prawdziwe intencje ich autorów, dlatego też w przypadku jakichkolwiek wątpliwości warto posługiwać się wersją angielską. W oryginale powyższy punkt brzmi:
8.1.1 Identification of statistical tools
Appropriate statistical tools for each process shall be determined during advance quality planning and included in the control plan.
Spróbujmy przeprowadzić szczegółową analizę sformułowań użytych w tym punkcie
1. podczas zaawansowanego planowania jakości (during advance quality planning)
Planowanie jakości to suma działań w wyniku których możemy dostarczać seryjne wyroby zgodnie z oczekiwaniami klienta. Podstawowym narzędziem nadzorowania planowania jakości jest według specyfikacji (7.3.1.a) harmonogram projektowy, który musi być podzielony na etapy (fazy). Kluczowymi etapami są: walidacja projektu procesu czyli pre-seria (a raczej wyniki z niej) oraz walidacja serii realizowana zwykle 3 do 6 miesięcy po SOP (7.3.1.b).
A więc sformułowanie „podczas zaawansowanego planowania jakości” należy rozumieć tak, że gdzieś, w którymś z etapów powinniśmy już znać wszystkie procesy choć może lepiej byłoby stwierdzić – wszystkie operacje i procesy technologiczne, służące wytworzeniu wyrobu. Możemy więc przyjąć że gotowy jest już flow-chart, rozumiany jako suma operacji od przyjęcia materiału do dostarczenia wyrobu do klienta (chyba że to sam klient odpowiada za dostawy do siebie, wtedy ostatnią operacją będzie załadunek). W różnych organizacjach ten element (flowchart) może być opracowywany w innych fazach czyli w innym miejscu harmonogramu.
2. należy określić dla każdego procesu (for each process shall be determined)
Jak już zaznaczyłem powyżej – operacja to działanie, które w wyniku daje zawsze charakterystykę lub kilka charakterystyk. To stwierdzenie choć banalne jest dość istotne ponieważ wyznacza oś, która powinna spinać dokumentację w całej przestrzeni tworzenia wyrobu. Tą osią jest charakterystyka. A więc „należy określić dla każdego procesu” powinniśmy interpretować w ten sposób, że dla każdej charakterystyki konieczne jest określenie narzędzi statystycznych.
3. odpowiednie narzędzia statystyczne (appropriate statistical tools)
Spróbujmy najpierw zdefiniować, czym są narzędzia statystyczne. Według Wikipedii metody statystyczne stosuje się wszędzie tam, gdzie chodzi o poznanie prawidłowości w zakresie zjawisk masowych. Dzięki zebranym danym można ustalić zmienność zjawisk masowych oraz tendencję ich przekształceń w czasie. Sporządza się w tym celu wykresy, ilustrujące krzywą rozwoju danego zjawiska czy też to, jaką stanowi część większej całości. Część danych dostarczają badania metodą grup reprezentatywnych.
Celem analizy statystycznej jest pozyskanie jak największej wiedzy z posiadanych danych. Aby zbiór danych był dobrą bazą do analizy statystycznej należy:
- zaplanować badanie i zebrać dane,
- podsumować zbiór danych z obserwacji, podkreślając tendencje, ale rezygnując ze szczegółów – czyli dokonać analizy np. wariancji, korelacji, regresji czy innych.
Tak więc musimy zbierać dane i dokonywać ich analizy i wyciągać wnioski o tendencjach (trendach) w charakterystykach lub też operacjach widzianych jako suma charakterystyk.
Jednym z najczęściej popełnianych błędów przez organizacje jest upraszczanie, czy też utożsamianie pojęcia SPC z kartą XR. Jednak metod statystycznych jest przecież wiele – np. karty np, karty c, karty CUSUM, karty PreControl, wykresy PARETO, które też są narzędziami do analiz, niekoniecznie pojedynczych charakterystyk mierzalnych, ale również poziomu wadliwości (występowalności błędów) w danej operacji. Analizą jest więc zarówno analiza zdolności procesu (czytaj charakterystyki) wyrażona współczynnikami Cpk czy Ppk, jak i analiza wadliwości operacji rejestrowana np. kartą np. mówiącą o ilości sztuk wadliwych w partii produkcyjnej na danej operacji (sic!).
4. odpowiednie (appropriate)
Najwięcej problemów interpretacyjnych stwarza słowo „odpowiednie”. Jeśli, jak stwierdziliśmy, punktem odniesienia jest charakterystyka, wówczas „odpowiednie” znaczy odpowiednie do analizowanej charakterystyki.
A z punktu widzenia realizacji wyrobu i procesu w charakterystyce najistotniejsza jest jej ważność (severity), którą najczęściej definiuje klient bądź organizacja. Stopień spełnienia wymagań związanych z charakterystykami ważnymi (bezpieczeństwa, krytyczne itp.) ma największy wpływ na satysfakcję klienta (zarówno zewnętrznego jak i wewnętrznego). Tak więc można przyjąć iż ważność powinna być jednym z najważniejszych kryteriów wyznaczania rodzaju (a więc odpowiedniości) metod statystycznych zastosowanych do analizy.
Oczywiście można przyjąć i inne kryteria kierując się metodyką FMEA, w wyniku której powinniśmy uzyskać zbiór najważniejszych dla nas charakterystyk, które należałoby objąć szczególnym nadzorem. Może to być kryterium SOD, SDO, może być top 10 RPN, może PARETO na RPN itd. itd. Mogą to być pojawiające się reklamacja wewnętrzne czy zewnętrzne dotyczące charakterystyki, których do tej pory nie uwzględnialiśmy w FMEA itd.
Przykładowy zestaw kryteriów zdefiniowanych przez organizację może wyglądać następująco:
- Dla charakterystyki bezpieczeństwa (SC) ważność (severity) powinno wynosić 9 lub 10, natomiast SPC powinno być prowadzone za pomocą karty XR
- Jeśli klient wymaga określenia zdolności procesu na badanej charakterystyce to sytuacja jest jasna – należy prowadzić kartę XR
- Dla charakterystyki krytycznej (CC) ważność powinna wynosić od 5 do 8, natomiast SPC może być prowadzone za pomocą karty XR lub karty np
- Dla charakterystyk standard ważność powinna wynosić od 1 do 4 i nie będziemy prowadzili bieżącej oceny charakterystyki, natomiast SPC może być realizowane jako wynik oceny danych z reklamacji wewnętrznych i zewnętrznych, pozwalających ocenić stopień tendencji wadliwości danej charakterystyki czy operacji.
Po co SPC?
W wyniku powyższych rozważań pojawia się następne pytanie: „Po co w ogóle analizować statystycznie?”. Odpowiedzi musimy szukać w specyfikacji ISO/TS.
W punkcie 05 czytamy że:
Celem niniejszej Specyfikacji Technicznej jest opracowanie systemu zarządzania jakością, który zapewnia ciągłe doskonalenie, ze szczególnym naciskiem położonym na zapobieganie wadom oraz redukcję odchyleń oraz redukcję ilości odpadów w łańcuchu dostaw (…)
Z powyższym stwierdzeniem jest zgodne wymaganie punktu 8.5.1.2 mówiące że:
Doskonalenie procesu produkcyjnego musi nieustająco skupiać się na nadzorowaniu i redukcji zmienności charakterystyk wyrobu oraz parametrów procesu produkcji.
Tak więc w wyniku analiz powinniśmy uzyskać potwierdzenie, iż proces produkcyjny, a tym samym charakterystyki produktu i wyrobu, są doskonalone zgodnie z metodyką PDCA.
Zwróćmy uwagę, że niektórzy klienci (np. FIAT) wymagają cotygodniowego dostarczania raportów Cpk dla wskazanych charakterystyk. Raporty te, prezentowane w formie wykresów, pokazują trendy współczynników zdolności. Ich wzrastanie jest dowodem na doskonalenie procesu. Jest to więc praktyczna realizacja wymagania zawartego w punkcie 8.5.1.2
Podsumowując, spróbujmy zdefiniować, czego może oczekiwać audytor w zakresie SPC przeglądając projekt dla konkretnego wyrobu. Przede wszystkim będą poszukiwane takie elementy, jak:
1. Harmonogram z podziałem na etapy.
2. Tabela kryteriów dla charakterystyk wraz z matrycą przejścia pomiędzy charakterystykami klienta a organizacji (gdyż optymalną sytuacją jest jeśli wewnętrzny system oznaczania charakterystyk jest ujednolicony, stały dla całej organizacji z odniesieniem do ważności oraz pozostałych kryteriów).
3. W którymś z etapów powinien pojawić się flowchart wraz z dodatkowymi informacjami, na przykład w formie następującej tabeli:
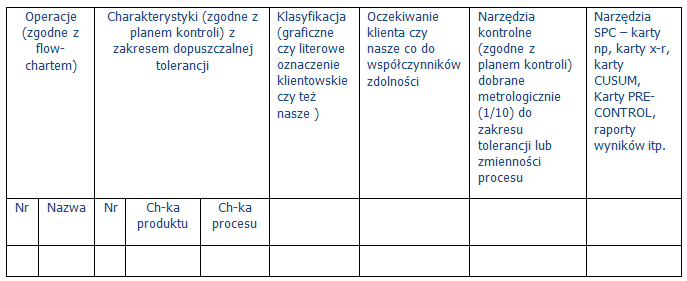
Takie rozwiązanie zapewni, że w zaawansowanym planowaniu jakości będą dobierane i włączane do planu kontroli odpowiednie (zgodne z ustalonymi kryteriami) narzędzia statystyczne.
JEDNAK
Największym problemem jest to iż najczęściej wyżej zdefiniowanych kryteriów – BRAK, standaryzacji podejścia do charakterystyk w FMEA – BRAK, kryteriów doboru sprzętu kontrolno-pomiarowego do charakterystyk – BRAK, itd. itd. itd.